Today’s completion operations are pushing the limits of layflat hose technology. As operators incorporate more produced water and additives into transfer lines, Select elected to reevaluate layflat hose technology from the ground up.
Three years ago, our research and development team began working on a modern design for layflat transfer hose, specifically designed for produced water applications. Develpment of this technology involved extensive analysis of lab tests, manufacturer collaboration, field trials, and comparisons with industry standards.
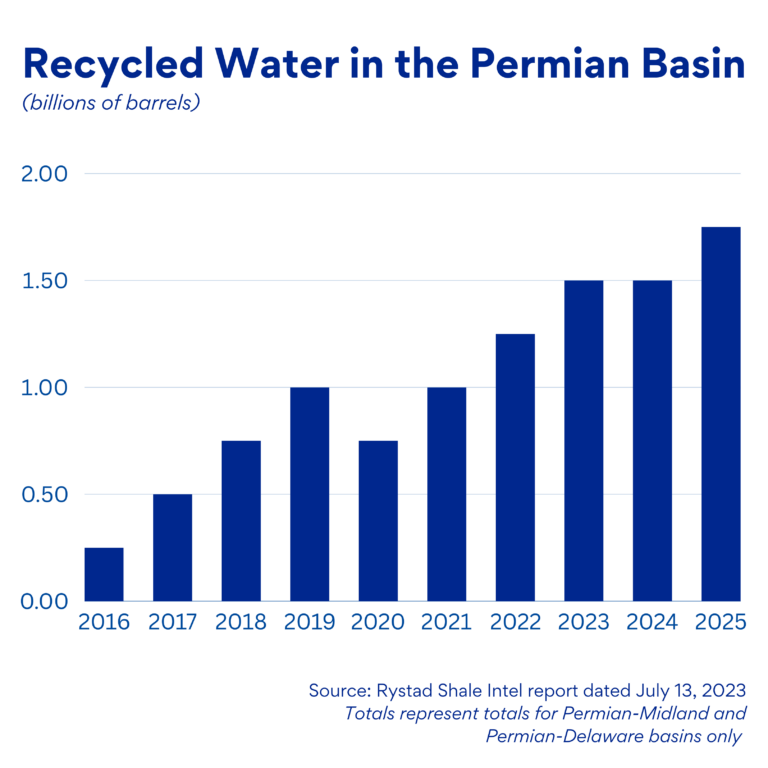
Why the Industry Needs a new solution for Water Transfer
The oil and gas industry is using produced water in operations more than ever before, requiring transfer solutions that can handle higher volumes and more challenging chemical compositions. Traditional layflat hose often struggles with the mechanical and chemical demands of these applications, leading to failures and inefficiencies. As the operational tempo and the use of produced water rise, there is a need for more robust, reliable, and chemically resistant hoses to provide safe and efficient water transfer.
Identifying Essential Design Requirements
To address these challenges, we identified four essential elements that a layflat hose needs to effectively manage produced and treated water in transfer lines:
- Chemical compatibility and mechanical wear resistance are required to withstand the harsh demands of produced water and treatment applications.
- Construction of the outer layer need compounds to improve UV resistance and reduce degradation from UV rays.
- Maintaining line integrity after frequent pressure cycles is critical for real-world operational conditions.
- Visibility into hose conditions and usage history, along with asset tracking using QR codes placed at regular intervals on the hose surface.
Partnership with Manufacturers
To meet these requirements, we called on the largest hose manufacturers in the industry. This collaboration focused on aligning product standards and challenging manufacturers to develop a product that meets the specific needs of produced water transfer operations.
- Material Selection: A six-month study led to the identification of two new materials with enhanced chemical resistance.
- QA/QC Protocols: We established detailed quality assurance and control protocols with our manufacturing partners, covering the entire production process. This initiative addresses inconsistencies and performance issues among major hose products, aiming to improve produced water handling in oil and gas operations.
Rigorous Testing Process
With samples of new hose material in hand, our in-house R&D team worked alongside third-party labs and trusted field partners to execute rigorous testing to identify which product performed best.
- Laboratory Testing: Techniques like microscope analysis, FTIR analysis, and material compatibility testing confirmed the integrity of the new hose materials.
- Field Testing: Fifteen miles of the redesigned hose were deployed in live jobs, receiving positive feedback. Short hose samples were tested in live projects over seven weeks, subjected to pressures ranging from 60 to 135 PSI. The hoses endured exposure to Permian Basin produced water with varying characteristics, including H2S presence and chemical treatments. Both cyclical fatigue and hydrostatic burst tests confirmed the hoses’ durability and performance, meeting or exceeding design specifications.
Impacts on the Industry
The results of our research and development will have significant impacts on the industry, enhancing operational efficiency, reliability, and environmental stewardship.
- Enhanced Reliability and Safety: Our proprietary product is designed for chemical compatibility and durability to mitigate the risk of failures, leaks, and environmental contamination, boosting operational reliability and safety.
- Improved Performance: Rigorous testing shows that our product has higher pressure resistance and chemical resilience, leading to increased productivity and cost savings.
- Standardization and Quality Control: Collaboration with major manufacturers and stricter quality control provides uniformity and adherence to industry standards, promoting greater reliability and interoperability.
- Technological Advancements: Features like QR code tracking and standardized design elements enhance usability and asset management, paving the way for future innovations such as higher-pressure hoses and advanced leak detection systems.
- Environmental Stewardship: This product contributes to sustainability in the oil and gas industry by reducing the risk of hose failures and environmental contamination.
Overall, Tideline™ is a significant step in advancing industry efficiency, reliability, and environmental sustainability. We are setting a new standard for hose technology, paving the way for continued progress and improvement in produced water management practices.
Today, we proudly have over 50 miles of Tideline™, a game-changing solution for last-mile water delivery, actively deployed in live jobs. As part of our ongoing commitment to innovation and improvement, we are continuously expanding its use across all produced water transfer operations, incorporating feedback and making enhancements to ensure optimal performance.